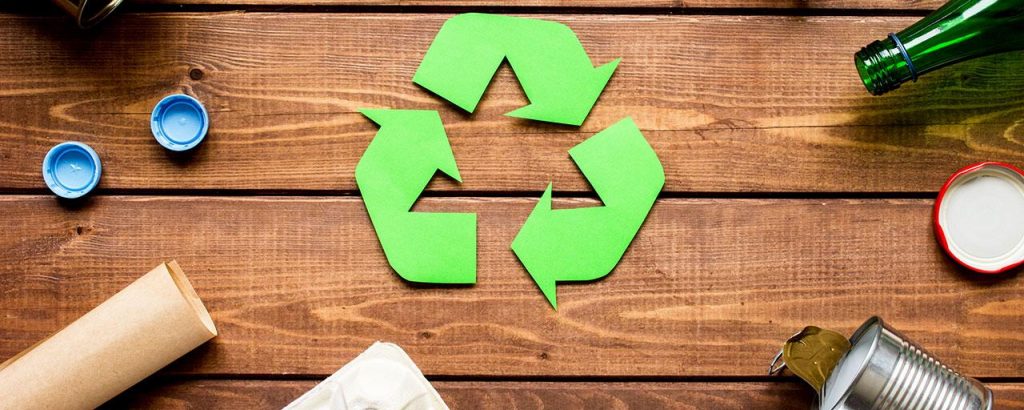
Despite the recent push toward recycling and “green” waste solutions, recovering valuable recyclable materials can be a challenge. Fortunately, recent advances in screening technology and equipment offer significant improvements in this area. With the right machinery, waste material can be sorted quickly and effectively. This means more valuable elements can be recovered, reducing both the financial burden and the environmental toll of waste. Additionally, improved screening can make it possible to recycle traditionally challenging materials. Here is an overview of some of the most pressing challenges in material recovery as well as a look at some recent advancements designed to address these shortfalls.
Challenges in Recycling and Material Recovery
Material processing is one of the areas where recycling challenges abound, especially in terms of municipal waste. In manufacturing, production byproducts often end up in the landfill rather than being recycled. Mining, construction, and demolition can also produce large amounts of waste despite the significant amount of valuable resources that could be recovered with the right equipment. Some of the difficulties include the following:
- Many materials/commodities can fall outside the standard sizing of sorting screens.
- High-moisture material can clog screens.
- Plastic film can wrap around screening equipment.
- Fibrous material can plug screens.
These are a few of the most prevalent challenges in material recovery and recycling that can significantly reduce the effectiveness of screening. New material processing equipment to address these problems usually focuses on increasing both efficiency and accuracy.
Recycling plastic (such as PET products) can be especially problematic, as the cost of recycling polymer material can be high. This means that in many cases, virgin polymer is less expensive than recycled material, leading many manufacturers to decline to purchase and use recycled polymer. Depending on the efficiency of the material screening technology, the recovered plastic material may be lower quality than new plastic. In terms of PET bottles, the goal of closed-loop recycling (manufacturing new PET bottles from recycled PET bottles) remains difficult to achieve. This can be due to a variety of factors including the cost of removing contamination to allow recycled material to be used in food-grade applications.
Disadvantages of Traditional Screening Methods
When it comes to the screening part of the material recovery process, there are several types of equipment available. One of the most common types of screening technology is a trommel screen. This type of equipment is essentially comprised of a cylindrical drum that is perforated. The drum rotates and is usually set at an angle to improve the flow of the material.
The perforations in the drum sort through the material, allowing small pieces to go through while forcing larger pieces to continue to move down the screen to the next stage. While trommels are somewhat effective and are fairly inexpensive, they are not very efficient. Based on the rotating design, only about a third of the screen is used at any one time. Additionally, it’s fairly easy for material to clog or bind the perforations, requiring frequent maintenance.
Vibrating screens, another common type of equipment, are known to have similar binding challenges.
Benefits of Advanced Disc Screens
Disc screens are designed to address some of the shortcomings of trommel and vibrating screens. In this type of equipment, there are several intermeshing, rotating shafts. The spacing between the shafts works to divide the incoming material into groups based on size. While older disc screen models sometimes have problems with clogging, newer screening technology counteracts this issue. Modern disc screens use octagonal discs, a shape that doesn’t have sharp points that can catch on long, fibrous, or stringy materials. Additionally, newer models isolate the material from the machine shafts to reduce the chance of clogging.
Advanced Technology and Efficiency in Material Processing
Processing and refining materials is another area where waste can be a problem. Advanced screening procedures and equipment can help reduce the amount of waste generated during processing. One of the most important aspects of advanced screening technology is the ability to sort material accurately and efficiently, reducing the amount of salvageable material that is mistakenly labeled as waste. Additionally, better screening can also reduce the amount of low-quality, unrecoverable material that remains after the screening process.
Improving the quality of material in the initial screening process can lead to a better final product. This is especially true when the materials being processed may be hazardous or difficult to recover. High-quality material processing equipment can also reduce the amount of environmental waste. Some of the most advantageous elements to look for in screening equipment include the following:
- Customization options that allow unique parameters for different materials.
- Technology designed to reduce the chance of clogging or binding.
- Configuration options to address moisture content.
- Equipment with a small footprint and low operational cost.
Better screening can eliminate impurities more effectively, leading to fewer quality control problems later on in the production process.
Additional Applications of Modern Material Screening Technology
Waste processing and recycling are perhaps the most well-known applications for advanced screening equipment. After all, the United States produced 262.4 million tons of municipal waste in 2015. Better recycling technology and awareness have contributed to an increase in recycling (from less than 10% in 1980 to over 34 percent in 2015).
Additionally, there are several other important applications. An efficient material screening process can help improve efficiency and reduce waste in a number of vital ways:
- Recovering reusable material from manufacturing waste
- Processing metals and other materials in mining operations
- Removing fines from production machinery
- Manufacturing sand
- Prescreening raw material prior to size reduction (crushing, grinding, etc.)
Material screening is vital to numerous industries, especially those related to waste reduction and recycling. Recent advances in science and procedures have led to modern equipment that is more effective. As material screening continues to improve, it should encourage more companies to leverage this technology in exciting applications.
[“source=manufacturing”]